MYOB Acumatica Manufacturing - Shop Floor Data Capture
Contents
MYOB Acumatica Data Capture technologies, Strategies and Considerations
Inventory and manufacturing data entry is historically time-consuming and prone to manual data entry errors. Paper based shop floor documents, inventory receipt documents, and other physical information must be captured promptly. This playbook provides manufacturers with an overview of available ADC technologies and a framework for planning and executing ADC implementation projects to streamline warehouse and shop floor data collection in a MYOB Acumatica project.
4 Easy Steps To Automated Data Capture Success
Introduction
Getting Started with Automated Data Capture - MYOB Acumatica
Growing companies coming off entry-level accounting systems lack fully automated data collection. They may have a tethered barcode reader for some inventory and manufacturing transactions, but they could do more if they had the right platform. Perhaps the company is looking to move off a legacy ERP system and already has a warehouse management system (WMS) or manufacturing execution system (MES) that they love, and they do not want to replace it. The great news is that it may already integrate with MYOB Acumatica.
MYOB Acumatica provides embedded barcoding and mobile capabilities to streamline data capture from a wide variety of devices. Automate pick, pack, and ship transactions; use data capture for receiving and put-away; move inventory throughout your warehouse or manufacturing shop floor; and use automated technologies for labor entry and material issues to production orders.
With MYOB Acumatica you have an adaptable and modular cloud ERP system ready for Industry 4.0 technologies such as artificial intelligence and machine learning. MYOB Acumatica easily connects to external systems making it a breeze to automate your business with plenty of choices in technology partners. You can start slow with barcoding, utilise the built-in mobile capabilities for clock-in and clock-out of production jobs, and leverage built-in automation features for backflushing and phantom bills of material – and then move into more advanced technologies such as RFID, voice-directed warehousing, machine interfaces, and full WMS or MES features.
“Before our ERP solution, our version of checking inventory was a sales guy running to the warehouse to ask how many units we had… Now we have location- based picking so anyone can bring the product into manufacturing…
Having our solution integrated with manufacturing allows us to manage all our inventory from a single location. We can easily look it up in the system and have confidence that it’s accurate.”
1. Automated Data Capture Technologies
Automation Options
In 1974, the first UPC scanner was used to scan a 10-pack of Wrigley’s Juicy Fruit chewing gum. Since then, automated data capture technologies have matured from barcodes to radio frequency identification (RFID) to PLC machine interfaces and artificial intelligence and machine learning to automate data capture that could only be imagined just a few decades ago.
“We’re constantly trying to automate things with the goal of minimal data entry... We want our solution to be quick and help us make as few mistakes as possible along the way to keep the customer happy—that’s what this business is all about.”
Paper-Based
Paper-based data capture is not entirely evil. It has a place in manufacturing and can be a cost-effective way to capture data for specific types of inventory and manufacturing transactions. However, it has many downsides and the goal for automation is speed and accuracy, something that cannot be carried out easily with paper.
MYOB Acumatica provides embedded document management and manufacturing reports.
PROS:
- Easy to implement
- Typically, very low cost
- Physical record of the data
CONS:
- Not real-time
- Requires manual data entry
- Prone to data entry errors
Barcode
Barcodes are among the most common data capture technologies. Barcodes come in many different styles and work with different devices including mobile devices, keyboard wedge devices, ruggedised tablets, and specialised scanners. Carefully consider the label format, label media, and printers used in harsh industrial environments.
MYOB Acumatica WMS & Manufacturing Data Collection provide out-of-the-box automation.
PROS:
- Compatible with most systems
- Relatively low cost
- Accurate data in real time
CONS:
- May require some data entry
- Some compatibility issues
- Requires configuration
RFID Tags
Radio frequency identification (RFID) provides passive data collection as tags on inventory pass near radio receivers. RFID has advanced with lower costs, improved accuracy, and the ability to capture more data such as temperature, triangulation of location, and even bacteria counts.
MYOB Acumatica Cloud xRP Platform with Open APIs facilitate fast and easy integration with RFID and other ADC technologies.
PROS:
- Accurate, real-time data
- Moderate costs after setup
- Minimal human intervention
CONS:
- Can be difficult to configure
- Higher initial investment
- Sometimes unreliable
ERP Features
Some ERP systems can simulate automated data capture. For example, backflushing captures data for labor and material transactions using pre-defined bills of material and routing standards.
Phantom bills of materials and after-the-fact production reporting are other common areas where ERP can streamline data capture.
MYOB Acumatica supports backflushing and phantom bills of material.
PROS:
- Easy to setup and use
- Typically, no cost (included in ERP)
- Fast and accurate data capture
- Requires minimal training
CONS:
- Can be difficult to configure
- Higher initial investment
- Sometimes unreliable
OCR Scan
Optical Character Recognition (OCR) technology recognises letters, words, and characters, captures data, and stores it in a system – typically a document management system. OCR is useful for external documents without barcodes.
MYOB Acumatica embedded document management combined with leading scanning applications provide great options for OCR scanning.
PROS:
- Easy to setup and use
- Typically, very low cost
- Good for external documents
CONS:
- Not real-time
- Some manual effort
- Some character recognition errors

Voice Recognition
Voice-recognition is relatively new for automated data capture. Manufacturers and distributors often use voice directed warehousing
(VDW) often with wearable technology to automate transactions including picking, packing, put-away, inventory movement, production reporting, and to search for information via chatbots and virtual assistants.
MYOB Acumatica is designed for use with AI Chatbots & Virtual Assistant technologies.
PROS:
- Easy to learn and to use
- Fast, hands-free data capture
- Accurate data in real time
CONS:
- Background noise issues
- Higher costs for configuration
- May require barcode scanners
Time Capture
Many time clock applications can be configured to collect data for shop floor labor reporting, and time entry for payroll and human resources. Biometric technologies enhance time capture by using fingerprints, facial recognition, or iris scans to validate who is posting the transaction.
MYOB Acumatica Manufacturing Data Collection captures clock-in and clock-out data for jobs.
PROS:
- You may already own them
- Moderate investment
- Easy to setup and to use
CONS:
- Some not compatible with ERP
- Biometrics can get costly
- May not work on mobile
Robotics, Scada, Plc
One cannot help but think of robotics when discussing automation. Robotics and machines capture massive amounts of data that can be stored using programmable logic controllers (PLC and hardware and supervisory control and data acquisition (SCADA) applications. They can
capture material usage, run times, and data such as temperatures, humidity, and more.
MYOB Acumatica open Platform provides fast integration with external sources including robotics, SCADA, or PLC through web services.
PROS:
- Fast and efficient data capture
- Additional data often available
- Typically, very reliable
CONS:
- Hardware can be expensive
- Configuration can be costly
- Some system compatibility issues
Mobile Devices
Historically mobile devices used in industrial environments included specialised and rugged scanners or tablets that affixed to forklifts or work centers. Newer mobile devices such as smart phones are becoming more common but may have some limitations compared to traditional scanners.
MYOB Acumatica Mobile Framework supports iPhone/IOS, Android, and other mobile devices.
PROS:
- Improved compatibility
- Relatively low cost
- Easy to setup and to learn
- Some system compatibility issues
- Many devices are not ruggedised for harsh industrial environments
WMS Systems
Warehouse Management Systems combine multiple technologies including bar coding, mobile, RFID, voice, and others into a cohesive system for automating inventory transactions and movement. This automation is done throughout the receipt, production, and shipping process as well as physical inventory counts, and more. Manufacturers
may use light WMS features inside their ERP system or integrate more advanced WMS applications.
MYOB Acumatica provides barcode printing on documents and reports and a light WMS system for automated inventory transactions.
PROS:
- Advanced automation
- Defined workflows and rules
- Integration with ER
CONS:
- More complex to implement
- Higher investment costs
- Dependent on other technologies
MES Systems
Manufacturing Execution Systems leverage other automation technologies in an advanced system to manage production including schedules, labour assignments, performance analysis, maintenance, quality, document control, and other manufacturing shop floor functions.
MYOB Acumatica is an adaptable platform designed for rapid integration to external systems.
PROS:
- Holistic and comprehensive system
- Fills many gaps in ERP capabilities
- Can have high return on investment
CONS:
- Expensive to purchase/license
- Complex to configure
- Can be difficult to use
AI / ML
Artificial Intelligence (AI) and Machine Learning (ML ) promise to improve many aspects of manufacturing including data capture. AI can be used to compare manually entered data against expected standards to validate data that is outside the expected norm. Machine learning can be used to improve on AI and other types of data capture.
MYOB Acumatica Alexa for Business and the Platform are designed for artificial intelligence and machine learning.
PROS:
- Validated data
- Potential for full automation
- Adaptable with human corrections
CONS:
- Not yet available for many systems
- Requires training to implement
- May have high investment costs
Lean Strategies
Lean manufacturing encompasses different strategies that lend themselves to automation. These include single minute exchange of
dies (SMED) for setups, Kanban for pull-based material transactions, and other strategies that work well with ADC.
MYOB Acumatica is an adaptable platform designed for rapid integration to external systems.
PROS:
- Many companies using Lean
- Compatible with most ADC technologies
- Generally low cost, high reward
- Few defined use-cases
- Technologies may interfere or conflict with lean objectives
“With our solution, someone can log in at any time, refresh the screen, and see live data on product to determine what product the team should focus on, rather than building things we may or may not need depending upon how demand has changed.”
2. ADC Assessment
Where Are You in Your ADC Journey?
The strategies you implement for automated data capture depend on how far along you are in your ADC journey. Manufacturers who are just starting will have few ADC processes in place using basic technologies. Manufacturers further along will have more automated processes using progressively more advanced technologies. The first step is to understand where you currently are before developing an ADC plan. Use the table and diagram below to chart your journey.
3. ADC Strategy
4 Steps to ADC Success
A successful ADC strategy starts with a solid foundation. It is critical to start with a modern ERP application that provides native data capture capabilities and an open architecture to connect advanced ADC technologies as you progressively automate data capture throughout inventory and manufacturing processes. Understand available options, research potential solutions, prioritise your initiatives, and develop a detailed plan for the project.
MANUFACTURING EXECUTION SYSTEM INTEGRATION
“Some of our operations are entering data live on the floor, so it accesses the production data and updates the inventory in real time which is key.”
Implementing ADC is easier when you build on a modern ERP system. It will be much more difficult and costly to implement ADC if you are using basic accounting or older ERP systems with few integration options and limited ADC application technology providers. BEGINNERS and NOVICES are typically moving to their first real ERP system. They should carefully consider their ERP platform. Even PROFESSIONALS and EXPERTS need to review their underlying ERP – especially if they are on an unsupported or legacy system.
Step 1
Foundation
Actions:
- Review Current ERP Features: What ADC features does your current ERP system provide? Does it support barcode printing and scanning for inventory and shop floor transactions? Does it require additional licensing or third-party applications? Are there limitations on the types of data you can capture or the methods you can use for data capture (e.g., barcode, RFID, OCR, or PLC)? Are features available if you upgrade or add new modules to your current ERP platform?
- Upgrade or Replace ERP: Consider upgrading or replacing your current ERP software before implementing ADC if your current ERP has limited ADC capabilities or the underlying technologies prohibit or restrict your ability to integrate with current and future ADC technologies and applications.
Step 2
Research
It is critical to research and document ADC strategies and technologies so you can prioritise initiatives and evaluate ADC solutions before developing a plan. Pay special attention to where you are in your ADC journey. The further along you are, the more opportunities there are to go back to improve previous ADC initiatives.
Actions:
- Research Existing Capabilities: Document ADC capabilities available inside your current (or potential replacement) ERP system. How are these capabilities used in the system today? Can they be improved, or should they be replaced?
- Identify ADC Initiatives: Develop a list of data transactions that you could automate with ADC technologies. Make notes on why these transactions would be good candidates for automation and what your process improvement goals are.
- Review Potential ADC Technologies: Contact your ERP partner to learn more about available technologies for automated data capture. Which technologies are available? Can they be integrated with your current or proposed ERP system? What are the costs for
licensing, installation, configuration, and training?
Step 3
Prioritise
Review existing ADC initiatives and look for ways to improve them. Rank initiatives based on cost and potential benefit from the list you created in Step 2. BEGINNERS need to start small with a few high-priority processes. NOVICES should look for new ways to expand on ADC technology investments. PROFESSIONALS and EXPERTS should improve processes with more advanced technologies in areas where they have yet to automate transactions or where new technologies can offer an improvement on earlier ADC projects.
Actions:
- Improve Existing ADC Processes: Review previously completed ADC projects. Often, you will find ways to improve data capture by implementing new features available from the technology providers or by replacing the ADC technologies with newer, more versatile solutions. Sometimes these improvements are more beneficial than implementing entirely new ADC projects.
- Implement New ADC Processes: You cannot automate everything at once so it’s important to use the prioritised list to formulate a plan. Consider those that can be implemented quickly using existing functionality in your ERP system or where you can use earlier investments in ADC technologies. Start with processes that provide the highest possible return on your investment first and work your way done the list to initiatives that provide less value.
Step 4
Develop A Plan
The final step in developing an ADC strategy is to document the implementation plan. The plan should include the desired goal of each ADC initiative and its supporting technologies, and a thorough timeline and process for conducting the implementation from start to finish. This
step is crucial for every manufacturer regardless of where they are in their ADC journey.
Actions:
- Goals & Desired Outcomes: Too many projects fail because the implementation strays from the initial goals outlined in the plan. It is vital to clearly outline the expected results. For example, you may want to reduce the steps it takes to capture data from 5 to 1. You
may want to reduce the time it takes to capture data by 80% for a defined transaction or process. Or you may want to reduce data entry errors by 90% for a process. Document the current state before implementing the ADC technologies so you have a benchmark to use as a measure of the success of the project. - ADC Technologies: Which ADC technologies will be used to automate the process? Sometimes this can be a single technology such as barcoding or a mix of technologies such as voice and barcoding used for inventory picking. Document which technologies will be used, dependencies and integration points with other systems, known limitations, and provider contacts for technical and consulting assistance.
- Timeline: The timeline for each initiative should be well-defined. You may not have a start date for the project, but you can develop the detailed phases required for the implementation with a timeframe defined to complete each step in the process. How long will it take to secure the technologies? How long will it take to configure them? How long will it take to test? How long will it take to train users? And how long will it take to go live on the new technologies
- Contingency Plans: Define contingency plans in case you run into technical issues or other conflicts that prevent the completion of the project. Consider running new ADC processes in tandem with earlier processes as a back-up.
ROBOTICS INTEGRATION
“Right now the exciting thing happening in addition to our solution is the introduction of robotics and automation to our industry and we recently have been able to introduce a couple robots who are going to be doing some of the labour here moving the plants around so that’s something we’re very excited about.”
Strategy Tips
Prioritising ADC projects can be difficult. Everything will seem equally important to automate and it is easy to give more weight to projects that are easier to implement rather than those that may take more time but could provide potentially higher value to the organisation. The following are some suggestions to consider when prioritising ADC projects with special consideration for where you are in your ADC journey.
“Carrying a multimillion-dollar inventory, you’ve got to have good controls for that...With the new controls that our solution has in place, our inventory is much more accurate.”
Simple
Some transactions lend themselves naturally to automation with low-cost technologies such as using native ERP features like backflushing or
simple ADC technologies like barcoding. BEGINNERS should start with ERP features and basic barcoding with keyboard wedge devices for a few processes while NOVICES may expand to more automated processes using advanced barcode scanners. Simple projects tend
to have a higher priority because they are low cost.
TARGET TRANSACTIONS
- Material transactions
- Job clock-in / clock-out
- Production entry (backflush)
- Inventory movement
- Inventory receipts
- Finished goods entry
Entry Error
All manual data entry activities are prone to error, but some are more apt to have problems due to the volume or complexity of the data. BEGINNERS should target a few transactions that are most prone to error while NOVICES should target multiple transactions with more complex data capture requirements. It is common to place a higher priority on transactions with higher volume of data capture or where the company has experienced significant data discrepancy issues in the past.
TARGET TRANSACTIONS
- Picking and put-away
- Shipment transactions
- Packing transactions
- Inventory adjustments
- Production entry
- Lot/serial transactions
Cost-Effective
Cost-effective transactions have a low investment in automation technology compared to the potential cost savings. As such, they
are among the first transactions to be automated. BEGINNERS can look for simple manufacturing and inventory transactions while NOVICES may look at more complex automation such as scale integration or lean manufacturing transactions. It is imperative to define the total cost and the desired outcomes to determine how cost-effective these projects really are.
TARGET TRANSACTIONS
- Material issues
- Labour entry
- Lean (Kanban)
- Warehouse transfers
- Inventory receipts
- Scale Integration
Time-Intensive
Some data entry takes more time than others. PROFESSIONAL ADC
users will begin to automate some time-sensitive transactions while EXPERT users will automate complex transactions that may require sophisticated technologies. It is important to document data capture
processes first. Then conduct research to understand how long each process takes to complete. It is only then that you can get a clear picture of how much time it truly takes to complete the process without ADC.
TARGET TRANSACTIONS
- Inventory receipts
- Machine downtime
- Inventory movement
- Shipment transactions
- Product returns
- Production entry
Time-Sensitive
Lags in data capture for many ERP transactions can cause serious inaccuracies for material planning, scheduling, and shipping. Time-sensitive transactions tend to be more complex. While all manufacturers will target time-sensitive transactions at various stages, PROFESSIONALS will begin to target a few time-sensitive transactions while EXPERTS will focus on a larger number of them with increased complexity.
TARGET TRANSACTIONS
- Inventory receipts
- Machine downtime
- Inventory movement
- Shipment transactions
- Product returns
- Production entry
“Our solution has an open platform, which was a huge selling point. The company looks for outside innovation and to work with as many ISV’s as possible to provide a multitude of solutions. We believe in that ethos because that’s how we operate.”
4. ADC Execution
ADC Implementation Phases
Now that you have a clear-cut, prioritised ADC plan in place – it is time to execute on the plan.
Execution covers four phases: Preparation, Go-Live, Review, and Continuous Improvement. Each phase is essential for the successful roll-out of new ADC strategies and the on-going maintenance and support required to ensure their long-term success.
Phase 1
Preparation
You need time to prepare for every ADC implementation. The time it takes to prepare will depend on the complexity of the project including the technologies used and the number of transactions you plan to automate.
For example, it may only take a few days to prepare for a barcoding project for a few inventory and manufacturing transactions. Conversely, implementing WMS, MES, or artificial intelligence and machine learning may require weeks or months of preparation.
In either case, preparation should start well before your desired go-live date and should include a review of the project plan with all project owners and contributors including internal staff, users, technology providers, consultants, and potentially vendors and customers if transactions are dependent on data they provide or if the data capture will impact their business processes.
Actions
- Plan Review: Review the implementation plan with the internal and external team. Make final adjustments as needed. Set the start date for the project and assign dates to each step in the implementation project. Define who owns each process and who contributes to each step. Consider the contingency plan and ensure that there is a process in case something goes wrong or resources become unavailable.
- Team Preparation: Notify all participants in the project of the timelines and their roles and responsibilities. Make sure they are available and trained on the technologies involved in the implementation. Do not forget to include external resources such as the technology provider, their solution consultants, and others who play a part in the project. You may also consider conducting a conference room pilot (CRP) and run through of the go-live implementation using a test system to further improve your chances for success as many issues are identified during the CRP exercise.
Phase 2
Go-Live Day
The plan has been set, it has been reviewed, the team is assembled and trained, and it is time to execute on the ADC implementation project.
A successful go-live is well-organised. One person should be identified as the project lead. Everyone else should be working with the project lead who orchestrates the steps in the project.
Actions
- Coordination: The project lead will orchestrate the implementation, delegating tasks to each team member and providing assistance or guidance throughout the project. They will make last minute decisions based on feedback from the team and they will chart the
progress of the project as tasks are completed. - Documentation: The actual go-live should be as close as possible to the planned implementation. However, it is inevitable that some last-minute changes happen along the way. Document what changes were made and why those changes were made so that you can review them after the implementation is complete.
Phase 3
Review
It may take a few days or even a few weeks for things to settle into place after you complete the ADC project.
Make sure to wait at least a week (preferably a month or longer) before reviewing the project. This will give users time to get used to the new processes while providing time to collect data to determine if the project was a success.
The review process should include notes from the go-live event, feedback from users, and early analytical results.
Actions
- Go-Live Notes: Review the go-live notes for details on last-minute changes to the project plan. Identify if there are any follow-up activities that need to happen to fine-tune the process or to address technology issues that occurred during the go-live.
- User Feedback: Talk to users of the new ADC technologies. What do they like about the technology and the new processes? Do they feel they are beneficial? Do they need more training? Have they embraced the processes? What do they suggest will make the process even better? You will often find that users have some of the best ideas if you take the time to ask them.
- Analytics: Now is the time to look at the early results from the project. Were you able to meet or surpass your goals? If not, why? And what can you do to improve the process so you can achieve the desired results? Develop a plan to capture data periodically to
continue analysing the results of the ADC project.
Phase 4
Continuous Improvement
An ADC project is never finished. You must continually monitor the results to ensure that employees do not slip back to previous processes. Technology upgrades and other issues can also change the effectiveness of the original ADC project.
Every ADC project must be maintained. There is always room for process improvements and new versions of the software or hardware that can provide more value while ensuring the technologies continue to function as expected.
You may also find new ways to reconfigure the process or ways to extend the project to automate even more data or other transactions.
Actions
- Monitor User Adoption: It is not unusual for users to fall back to old processes even if they initially appear to be on board with the new plans and procedures. Monitor user activity periodically to identify users who have embraced the new processes and those who need
more encouragement. You may also consider disabling manual data entry or limiting access to alternative data capture methods for certain users after the successful go-live on the new ADC technologies. - Maintain Technologies: Stay current on the latest updates and versions of your ERP software and connected ADC technologies. Setup a sandbox for testing upgrades to ensure compatibility before upgrading live production systems. Review product road maps and talk to technology partners to understand the lifecycle for the technologies you have implemented. They may drop support for some critical technologies, or they may provide a
better option as a replacement to your current technologies. - Improve Processes: Managing technology implementations is no different than implementing lean Kaizen and other continuous improvement projects. Utilise the same methodologies to seek out ways to improve processes – even those that have already been
automated with ADC. - Explore New Opportunities: There is always a process that can be automated – ALWAYS! Continue to look for new ways to extend your ADC investment to other types of data as your organisation moves from Beginner to Novice, to Professional to Expert stages. Take on more complex ADC projects and consider more advanced technologies as they become available

EXECUTION TIPS
Managing ADC implementations can be difficult without the right tools. MYOB Acumatica includes a Project Management module to plan for ADC projects with integrated Case Management and Support to manage support activities, Wikis for documenting policies and procedures, and even Field Service for managing technology installations, upgrades, and other project-related activities.
“ERP deployments have a very high failure rate. But we did in fact launch half the system exactly on time and half the system one day late which is rare and the project overall over the last year we’ve been using it has come in right around on budget which is also very rare.”
Projects
MYOB Acumatica includes a Project module that is perfect for setting up and managing automated data capture and other internal IT or manufacturing projects. You can define project budgets, create tasks with planned and actual start and end dates, assign a project manager, manage project resources, track project costs (with direct integration to Purchase Orders and PO Requisitions for purchased
equipment and services allocated directly to the project), and provide for employee time and expense entry with mobile scanning for receipts, keeping all the information you need in one system.
Service Requests
MYOB Acumatica Case Management integrates with Service Management for larger manufacturers who need to schedule services, upgrades, and other IT activities for installed technologies, hardware, and
applications. Service Management provides service tickets, technician scheduling and dispatch, mobile time and service order accessibility, and a whole lot more.
Support Cases
Use the MYOB Acumatica CRM suite to manage support cases for installed technologies such as Automated Data Capture or for issues related to the implementation itself. Cases can be related to projects,
accounts, and contacts, and keep critical information connected. Cases are assigned to an owner in your help desk with date fields for when the issue was reported and resolved, severity and priority codes, and status.
Document case activities with notes. You can even attach files and setup notification workflows to keep everyone in the loop.
Wikis
By using MYOB Acumatica wikis, users create, edit, and share information. Wikis are ideal for documenting use-cases for ADC and other technologies. Develop procedure manuals, embed training videos, attach user manuals, and share everything with employees and external business partners or consultants. Wikis provide version tracking and security.
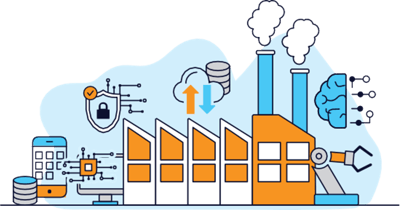
Automated Efficiency with MYOB Acumatica
We are currently on the precipice of a new era in automated data capture. While many companies are just starting with barcoding, RFID, and basic automation available in their ERP systems, others are
implementing sophisticated technologies including PLC/SCADA, WMS, MES, artificial intelligence, and machine learning.
ADC drives efficiency throughout manufacturing and inventory processes making data entry faster and more accurate. Manufacturers in every stage of their ADC journey can improve processes by setting a
solid ERP foundation, researching available technologies, prioritising ADC initiatives, and developing a detailed project plan. ADC project success is dependent on preparation, systematic go-live activities,
on-going reviews, and continuous improvement of both processes and technologies.
MYOB Acumatica Manufacturing Edition is a future-proof, cloud ERP application built on a modular and adaptable platform with native automated data capture and open APIs for rapid integration with
external data capture devices and systems to help manufactures thrive in the new digital economy. MYOB Acumatica is designed for midmarket manufacturers that struggle with disparate, siloed systems for production, CRM, warehouse management, field service, financial, and business intelligence applications by providing an end-to-end business management solution that can be accessed in the cloud using a standard web browser or mobile application with built-in barcode scanning.
Overall MYOB Acumatica Cloud ERP is a comprehensive business management solution that was born in the cloud and built for more connected, collaborative ways of working. Designed explicitly to enable small and mid-market companies to thrive in today’s digital economy, MYOB Advanced flexible solution, customer-friendly business practices, and industry-specific functionality help growing businesses adapt to fast-moving markets and take control of their future.
For more information on MYOB Advanced visit: MYOB Acumatica - Cloud ERP